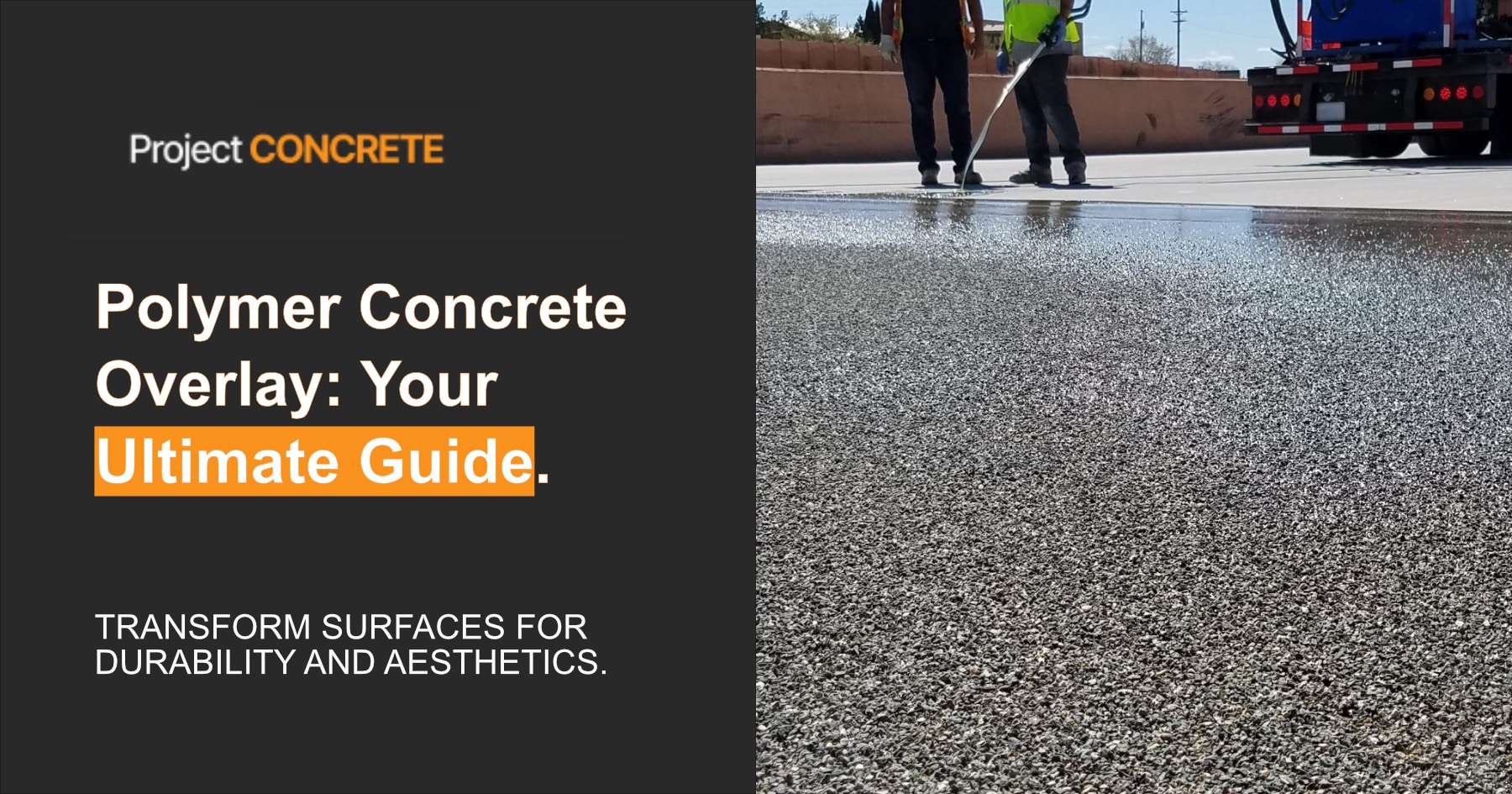
Welcome to the amazing world of polymer concrete overlay. This is where good looks meet toughness. This game-changing coating can freshen up your concrete spaces and make them even stronger. Sounds interesting? Let’s dive in.
Key Takeaways
- Polymer concrete overlays provide a durable and flexible 2-4mm thick coating over existing concrete, yielding improved adhesion and strength, and they’re suitable for rapid revitalization of worn surfaces.
- The installation of polymer overlays requires preparatory tasks such as cleaning, damage repair, and use of correct ratios for mixing, followed by skilled application to ensure strong bonding and seamless finish.
- Polymer overlays offer extensive design versatility through stamping, texturing, and colouring techniques, making them suitable for residential, commercial, and industrial applications with an average lifespan of 25 years or more when properly maintained.
Understanding Polymer Concrete Overlays
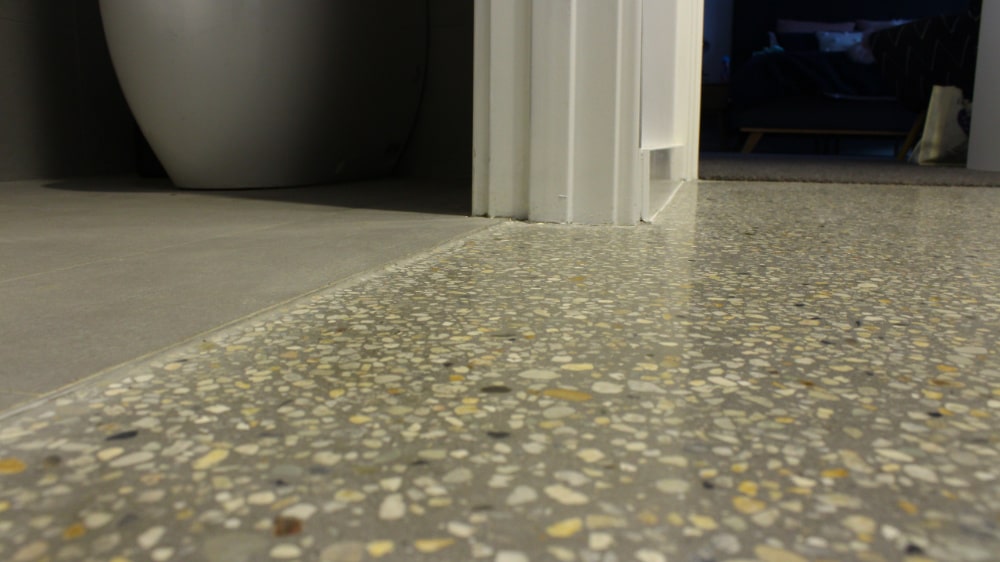
Imagine a thin, durable coating that adorns your existing concrete floors or exterior concrete slabs, enhancing not just their appearance but also their properties. That’s Polymer Concrete Overlays for you. These overlays are part of the Polymer Modified Cementitious Overlay Systems, enabling thin applications with a depth of 2-4mm while offering improved adhesion, strength, and durability.
The ability of the existing concrete to act as a base for the overlay is a key consideration. A structurally sound concrete slab, free of gapping cracks, severe delamination, and an unstable subbase, makes a suitable candidate. These overlays are chosen for their capacity to revitalize worn or unimpressive concrete into a decorative and refreshed surface swiftly, often within a day.
Composition of Polymer Concrete Overlays
Each component of polymer concrete overlays contributes significantly to the creation of a smooth, durable surface with superior strength. The mix comprises:
- A resurfacing compound, which provides a sound surface for the overlay on the existing concrete slab
- The polymer itself, which enhances the strength, flexibility, and adhesion
- Colour pigment, which adds colon and aesthetic appeal
- Water, which facilitates the mixing and application.
Liquid polymers are high-performance, cost-effective, and convenient materials that grant the overlay exceptional:
- durability
- flexibility
- toughness
- favourable mechanical properties
The colour pigments, incorporated into the composition, provide the intended colour throughout the overlay, enhancing the visual appeal and making the overlays a perfect solution to repair and enhance spalled concrete surfaces.
Benefits Over Traditional Concrete
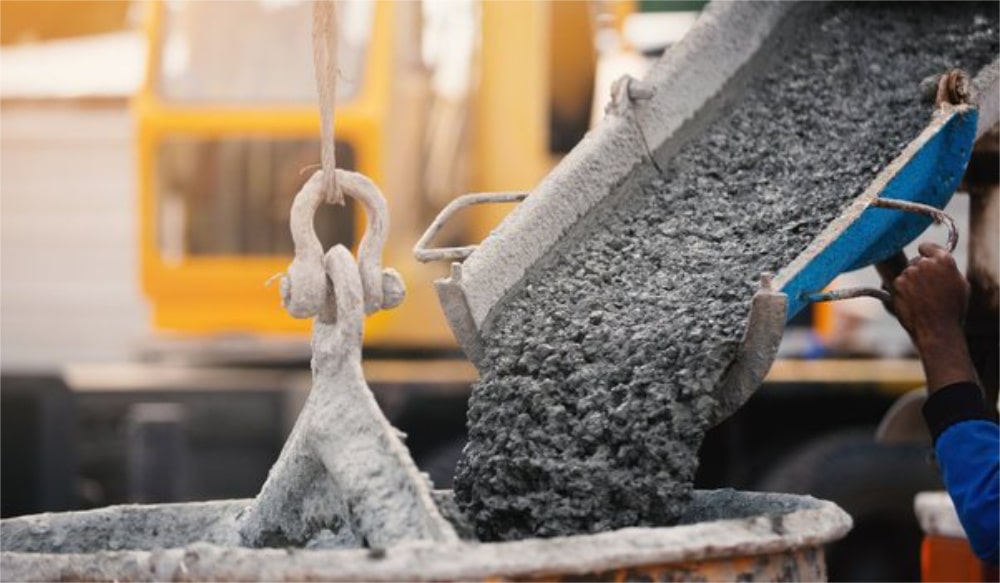
When compared to traditional concrete, polymer modified concrete overlay is present numerous advantages, including that polymer overlays cure fast. They provide significantly improved adhesion by utilizing a specially prepared mix that incorporates specialty cement with enhanced tensile and bond properties, along with high-performance polymers, ensuring a robust bond with the existing surface.
These overlays offer superior flexibility and durability compared to basic cement-based overlays. They are not just a thin layer glued to the surface; they are a high-performance blend with polymers, such as natural rubber latex, that provide superior flexibility, allowing for movement without cracking and ensuring greater durability.
Polymer overlays also exhibit enhanced resistance to weather elements, reducing long-term damage and making them a suitable alternative to traditional flooring materials like linoleum tile in certain applications.
The Installation Process
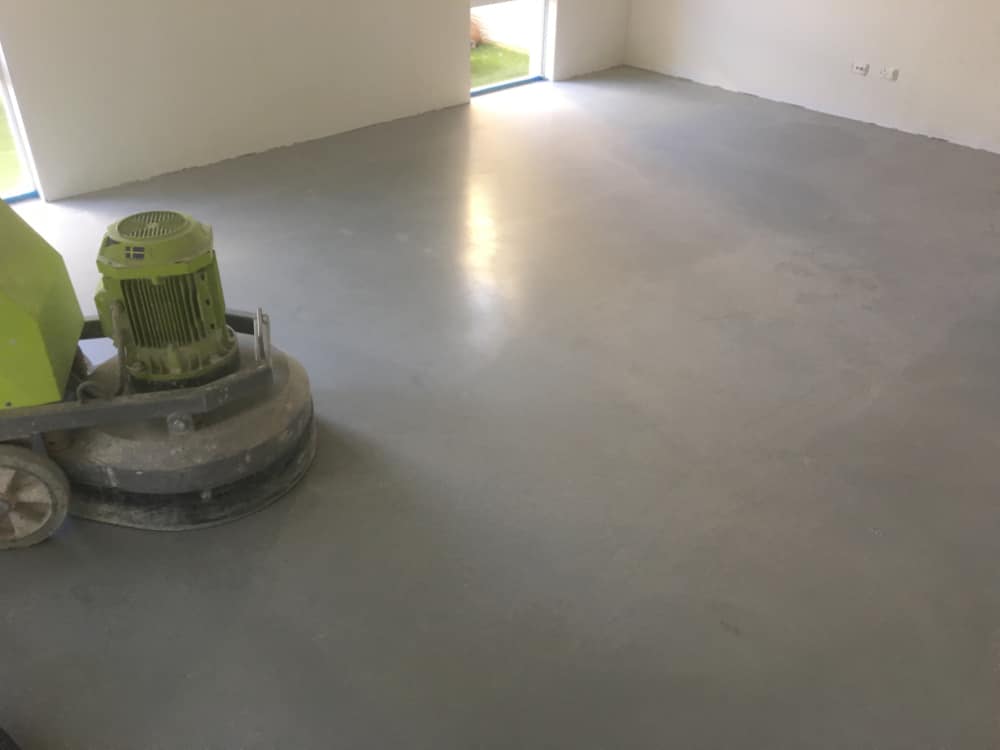
To successfully install polymer overlays, thorough surface preparation and skilled application techniques are necessary. These overlays are a popular choice for decorative concrete applications due to their versatility in design and the ability to transform existing surfaces into visually appealing and durable solutions.
To facilitate strong bonding of the overlay, correct surface preparation is of utmost importance. A qualified contractor can be located through lists of approved installers provided by product manufacturers and distributors, who have typically completed a comprehensive training program. For those aspiring to become an installer, many distributors offer training courses throughout the year, tailored to specific needs.
Surface Preparation: Key to Success
Thorough cleaning and correct repair of cracks during surface preparation is vital for the successful adhesion of the overlay. The process includes:
- Removing loose debris
- Using a pressure washer to eliminate stubborn stains
- Applying degreaser for any oil or grease spots
- Repairing any damage
- Ensuring the surface is thoroughly dry.
The materials required for surface preparation may encompass:
- Power washer
- Concrete grinder or scarifier
- Crack repair materials
- Bonding agent
- Primer
- Tools for mixing and applying the overlay such as a trowel or squeegee.
Meanwhile, various techniques such as re-vibration or mechanical re-trowelling, epoxy injection, routing and sealing, grouting, stitching, and drilling and plugging can be employed for crack repair.
Applying the Overlay
Preparing the mix is the initial step in the overlay process. The recommended mix ratio may vary depending on the specific application and temperature. It is advisable to consult the mix design guidelines provided by the manufacturer for the recommended mix ratio and initiator percentage.
The application process involves a power trowel, a paddle mixer, and a corded drill. The steps to ensure a seamless application include surface preparation, application of a bonding agent, mixing the polymer concrete overlay, applying the overlay, smoothing out any imperfections, and allowing proper curing time. The overlay generally requires 2-4 hours to dry.
Design Flexibility and Aesthetic Appeal

Polymer overlays offer a wide array of design options, promising remarkable design flexibility and visual appeal. Their versatility extends to various stamping, texturing, and colouring techniques, all of which play a role in enhancing their design flexibility.
Whether you want to replicate the appearance of:
- tile
- flagstone
- block
- other natural shapes
The trowel down finishes can achieve it. Alternatively, a spatter finish results in a tactile, multi-colored surface that is well-suited for poolside areas. Moreover, coloring techniques, such as acid stains and integral pigments, expand the range of aesthetic options available, allowing for customization and playing a role in the overall attractiveness of the overlaid surfaces.
Stamping and Texturing Techniques
Imprinting a pattern onto the still-plastic surface of the overlay using a series of mats and/or texture rollers results in a stamped finish. This technique gives the appearance of materials such as:
- sett paving
- old bricks
- weathered timber planking
- natural stone slabs
The application of texture to polymer concrete overlays involves incorporating pattern, texture, and color into exterior concrete slabs using polymer-modified overlays that are specifically created to improve the surface’s visual appeal. Employing the highest quality colouring systems can yield a multi-tonal finish with just one application of the colourant, thereby greatly enhancing the visual intricacy and attractiveness of the stamped finish on polymer concrete overlays.
Coloring Options: From Acid Stain to Integral Pigments
The world of coloring options for polymer concrete overlays is vast and vibrant, ranging from:
- Spray-down toppings
- Skim coats
- Self-leveling overlays
- Concrete overlay stains and dyes
One interesting process is acid staining, where an acid-based solution is applied to the surface of the overlay. The acid reacts with the minerals in the concrete, creating a chemical reaction that produces unique and variegated colors. This process results in a translucent, mottled appearance that enhances the aesthetic appeal of the overlay.
Integral pigments are incorporated into the concrete mixture prior to application as an overlay. These pigments integrate into the concrete, adding color throughout the entire thickness of the overlay, and are utilized to enhance its visual appeal. The selection of a color should take into consideration factors such as final color goals, decorative coarse aggregates, and specific needs in order to achieve the desired aesthetic and functional outcome.
Where to Use Polymer Overlays
Polymer overlays are suitable for a wide array of applications, both in residential and in commercial settings. In the cozy confines of your home, they can revamp:
- Concrete floors
- Driveways
- Patios
- Pool decks
Their prowess isn’t just confined to homes; these overlays also demonstrate remarkable performance in high-traffic areas such as malls or airports, offering enhanced wear resistance and durability.
Moreover, they also find application in industrial settings. They rejuvenate deteriorating concrete floors, providing a resilient and enduring surface remedy while minimizing operational disruptions. They are known to endure constant heavy traffic and last for up to 25 years or more when installed and maintained properly.
Residential Applications
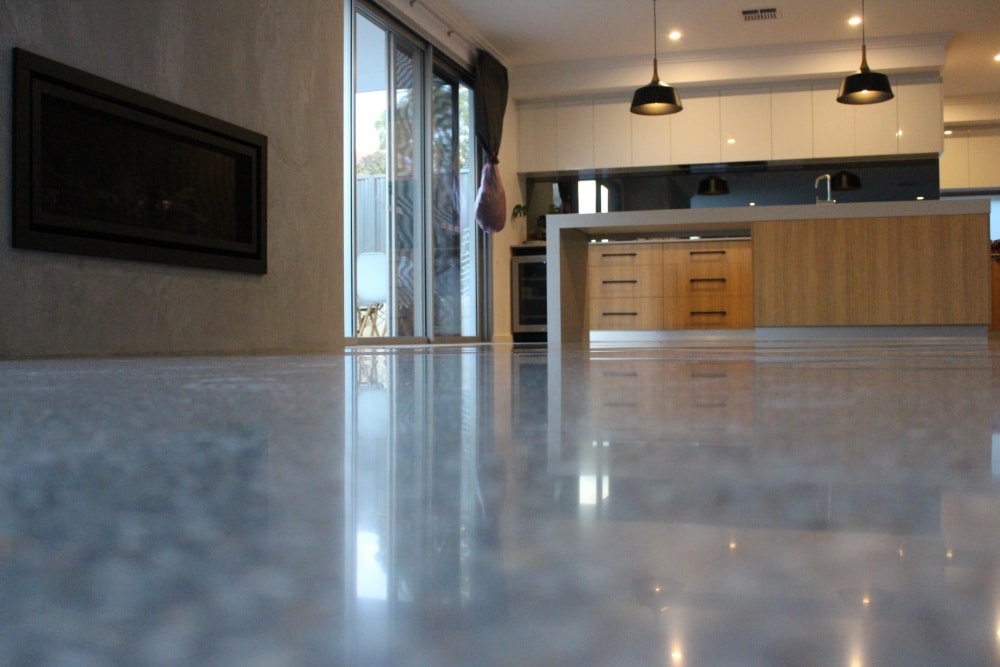
In residential settings, polymer concrete overlays serve both practical and aesthetic purposes. They enhance structural integrity and can withstand heavy traffic, offering twice the durability of traditional concrete. So, whether it’s a patio or a driveway, these overlays can handle it all.
Moreover, overlays can be used for decorative coatings such as Sundek and Sunstone, as well as stamped and stained concrete or epoxy floor coatings. They can be supplemented with additional top coatings like epoxy or acrylic to further enhance and protect the surface. However, there are potential disadvantages such as higher costs, limitations in appearance, and vulnerability to damage such as cracking or chipping, particularly from environmental elements like sun and UV exposure.
Commercial and Industrial Uses
In the commercial and industrial world, polymer overlays hold their ground firmly. They rejuvenate deteriorating concrete floors, providing a resilient and enduring surface remedy while minimizing operational disruptions. The significant cement and polymer content in these overlays are key factors contributing to their enduring performance.
With remarkable longevity, polymer overlays in high-traffic commercial areas can endure constant heavy traffic and last for up to 25 years or more when installed and maintained properly. However, in areas with heavy machinery, the overlays’ resistance may be compromised, as they can exhibit a reduction in flexural strength after exposure to aggressive conditions.
Nonetheless, their aesthetic appeal is undeniable, and they can effectively transform not all existing concrete floors, but a majority of them, into visually appealing interior floors, thereby enhancing the overall aesthetic appeal of commercial spaces.
Maintenance and Longevity of Polymer Overlays
By maintaining and caring for polymer overlays properly, their lifespan can be extended, guaranteeing prolonged performance. Regular maintenance and inspection are essential to uphold their longevity and performance. The frequency of these activities can vary based on factors such as overlay condition, traffic levels, and project-specific requirements.
The recommended maintenance practices for polymer concrete overlays include:
- Assessing the concrete surface prior to overlay application
- Ensuring correct installation
- Routine cleaning and maintenance activities, such as sweeping and washing, to extend the overlay’s lifespan
- Taking weather factors into account during installation and maintenance to optimize the lifespan of polymer concrete overlays.
Routine Care
Adopting routine care practices like frequent cleaning and occasional resealing can safeguard the overlay and assure its durability. For routine maintenance cleaning, it is advisable to use a pH neutral chemical cleaner, or a mixture of warm water with soap, or an all-purpose cleaner as safe options.
Resealing polymer concrete overlays is another important aspect of maintenance. This process requires thorough surface preparation, including evaluating the condition of the concrete and ensuring cleanliness. After applying the overlay, it is crucial to allow the concrete to cure undisturbed for a minimum of 24 hours before proceeding with sealing and protection.
The overlays should be resealed every two to three years, taking into consideration the extent of wear they experience.
Dealing with Wear and Tear
Dealing with wear and tear, including minor cracks and chips, is an unavoidable aspect of the lifecycle of polymer overlays. It’s crucial to identify typical indicators of deterioration like:
- cracks
- unevenness
- spalling
- white and milky appearance of the sealer
- surface texture issues.
Minor cracks and chips can be repaired by following these steps:
- Assess the damage using suitable tools.
- Clean the affected area.
- Apply a polymer-modified Portland cement mortar overlay.
- Smooth out the applied overlay to blend with the surrounding area.
- Leave it to cure according to the manufacturer’s instructions for a seamless finish.
Preventive measures to minimize wear and tear include applying a protective sealer post-curing and controlling moisture issues.
Troubleshooting Common Issues
Like all materials, polymer overlays are also subject to common problems. One such issue is cracking, which often results from movement in the underlying concrete slab. Cracks can still appear through the overlay system, but their appearance can be mitigated by incorporating saw cuts or profiles in areas prone to cracking or expansion joints, which allows for movement and helps minimize the potential for cracks to develop in the overlay.
Repairing Cracks
Cracks in polymer concrete overlays can be a result of the normal shrinkage of the concrete during hardening and drying, overwatering of the concrete at placement, and the transfer of cracks from the underlying surface. These cracks can be repaired by cleaning the crack, preparing it, applying a primer, filling the crack with the chosen material, smoothing the finish, and sealing the repair.
To prevent future cracks, one can:
- Incorporate an anti-fracture membrane during preparation
- Conduct proper repairs on existing cracks
- Ensure the extensibility of the overlay material used
- Select a flexible concrete polymer for the overlay composition.
Addressing Substrate Movement
Substrate movement refers to the shifting or displacement of the underlying concrete substrate. It can result in cracking, delamination, and bond failure between the overlay and the substrate. To mitigate substrate movement, one strategy is to ensure that the overlay is a minimum of 3/8” (9.5mm) thick. Another approach involves designing portland cement concrete or polymer concrete overlays for periodic replacement.
The utilization of anti-fracture membranes can help address substrate movement as they bridge small cracks in the subfloor, preventing them from propagating up through the tile and grout. These membranes serve as a barrier, isolating the tile from any movement or cracks in the substrate, and thereby safeguarding the tile installation from the detrimental effects of substrate movement.
Summary
In conclusion, Polymer Concrete Overlays have revolutionized the way we perceive and utilize concrete. From their exceptional design flexibility and aesthetic appeal to their enhanced durability and longevity, they stand as an excellent choice for both residential and commercial applications. With careful installation, regular maintenance, and effective troubleshooting, these overlays promise to transform your spaces with a touch of elegance and a promise of endurance.
Don’t let worn-out, dull concrete spaces dampen the aesthetics of your home or business. It’s time to breathe new life into your concrete surfaces with our advanced Polymer Concrete Overlays.
At Project Concrete, we’re committed to providing high-quality, durable, and aesthetically pleasing solutions for your concrete surfaces. Our Polymer Concrete Overlays not only revamp your space but also enhance its durability and longevity.
So, are you ready to take the leap and transform your space? Contact us today and let’s start your journey towards a more visually appealing and enduring concrete surface.
Jonathan Blackburn
January 4, 2024
Social Media